Lean Caps refer to a concept typically found in the context of lean
manufacturing or lean management practices. In these frameworks, "caps"
often relate to limiting or controlling the amount of work or resources
being used at any given time to ensure efficiency, minimize waste, and
optimize processes. The "lean" approach emphasizes the reduction of
waste, whether that be time, materials, or labor, by focusing on
value-creating activities and continuously improving processes.
A
"lean cap" might refer to a cap or limit placed on certain metrics or
resources, such as limiting the number of items in a production batch,
the number of tasks being handled at once, or the capacity of a
particular process. This helps in preventing overproduction, which is
one of the major forms of waste in lean methodology. By setting these
caps, organizations can ensure that resources are allocated in a
balanced way, demand is matched with supply, and production is kept at
an optimal level to meet customer needs without excess.
Uses:
Lean
Caps are used in various industries to enhance operational efficiency,
reduce waste, and create smoother workflows. In manufacturing, one of
the primary uses of lean caps is to control production volume, ensuring
that only the necessary amount of products is produced at any given
time. By limiting the number of items being manufactured, companies can
avoid overproduction, which leads to excess inventory and unnecessary
storage costs. This helps to optimize space and resources, as well as
reduce the chances of product defects caused by rushed or excessive
production processes.
In the context of service industries, lean caps
are used to manage workloads and prevent bottlenecks in processes. For
example, in software development, lean caps can limit the number of
tasks in progress to ensure that team members are not overloaded,
promoting better focus and faster delivery. By capping the work in
progress (WIP), teams can reduce the time spent switching between tasks
and allow for more efficient problem-solving and decision-making. This
approach helps maintain high levels of productivity and prevents burnout
or errors due to overwork.
In healthcare, lean caps are often
used to streamline patient flow and manage the capacity of medical
staff. Hospitals may implement lean principles to limit the number of
patients admitted at any given time or to regulate the number of
procedures scheduled, ensuring that resources such as staff, equipment,
and space are utilized efficiently. This helps avoid overcrowding,
reduces patient wait times, and ensures that the quality of care remains
high. Lean caps thus support a balance between supply and demand,
helping organizations provide better services without overwhelming their
systems.

How to use:
To
effectively use the concept of Lean Caps in paragraphs, you can
incorporate them into the broader context of operational strategy or
process improvement. Here's how to do so:
Introduction of Lean Caps:
Begin by briefly explaining what Lean Caps are, especially in the
context of the industry you're discussing. This gives your reader a
solid foundation and understanding of the concept.
Example:
"Lean
Caps are a key principle within lean manufacturing and process
optimization strategies. They involve placing limits or restrictions on
certain processes or resources to prevent inefficiencies such as
overproduction or bottlenecks, ultimately promoting a more balanced and
efficient workflow."
Specific Use or Application:
Next, describe how Lean Caps are specifically applied within a
particular industry or process. This could involve real-world examples
of how they are used to manage resources, production volume, or
workloads.
Example:
"In manufacturing, Lean Caps are often used
to control the amount of product being produced at any given time. By
limiting production volumes based on actual customer demand, companies
prevent excess inventory and reduce the costs associated with storage
and waste. This not only improves the bottom line but also helps
streamline supply chains."
Benefits or Impact:
After explaining how Lean Caps are used, discuss the positive outcomes
that result from their implementation. This could include increased
efficiency, cost savings, or higher quality products.
Example:
"The
use of Lean Caps in this manner leads to a more responsive production
process, where resources are used optimally and waste is minimized. By
avoiding overproduction, companies can reduce storage costs and improve
the flow of materials, ultimately resulting in faster delivery times and
higher customer satisfaction."
Broader Implications or Long-Term Use:
Conclude by addressing the long-term impact or the broader
applicability of Lean Caps. This might include their role in continuous
improvement or how they can be adapted across different industries.
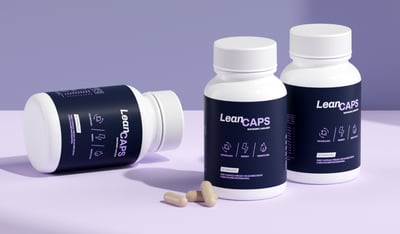
Conclusion:
In
conclusion, Lean Caps are a powerful tool within lean management and
operational efficiency strategies, helping organizations control
production volumes, workload, and resource allocation to minimize waste
and optimize processes. Whether in manufacturing, software development,
or healthcare, implementing Lean Caps enables businesses to maintain a
balance between supply and demand, improve productivity, and ensure
high-quality outcomes. By setting clear limits and fostering a culture
of continuous improvement, Lean Caps contribute to long-term
sustainability, cost savings, and enhanced customer satisfaction.
Ultimately, their thoughtful application can drive organizations towards
greater efficiency and success in an increasingly competitive and
fast-paced market.